Leading Thermal Paper Slitter Rewinder Machine Manufacturer
- Competitors sometimes refer to our design
- Clients help us shoot promotion videos
- Choice of Portugal famous brand Navigator
- Customer service footprint across the world
Thermal Paper Slitter Rewinder Machine
Thermal Cash Register Paper Slitter Rewinder is always Jota’s core product from the very beginning.
Jota thermal paper slitting machine’s iconic clients include Navigator, SS Labels, K.M.S Group, etc.
When you are shopping in the supermarket or having dinner at a restaurant and swiping your credit card, there is a small cash roll of paper,
which is very popular nowadays. It is thermal reception paper or thermal cash register receipt paper.
There is a great demand for this kind of paper in the current market, and it penetrates all aspects of your life.
Therefore, the thermal paper slitting conversion should be a good business for you, it is with a small investment and quick return.
As a professional thermal paper slitter rewinder machine supplier, after 20 years of industry precipitation, we could now provide a full set of
thermal paper cashier receipt solutions chain from A to Z, from base thermal paper mother roll, paper core (plastic core), thermal paper
slitter rewinder Machine, thermal paper printing machine, cash roll finishing wrapping line, and packaging film, we could provide a full set
of professional solutions.
Submit your requirements now, we will recommend a suitable thermal roll-slitting machine to you.
Jota Machinery: Your Trustworthy Thermal Paper Slitting Rewinding Supplier in China
Jota is a dependable supplier of slitter rewinders for thermal paper; we have our own factory and CNC center.
We can provide a comprehensive solution for your thermal paper roll business.
To obtain a quote for your desired thermal paper roll machine, please submit your request.
Machining Material
- Visible high-quality components
- Famous brands such as Siemens, Yaskawa, Delta, Schneider, Mitsubishi
- Self-supporting CNC processed sheet metal, precision parts
- Assembly raw materials provided by long-term cooperation suppliers
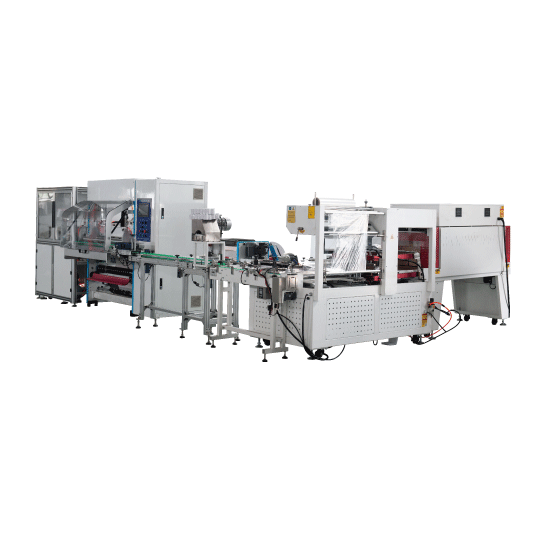
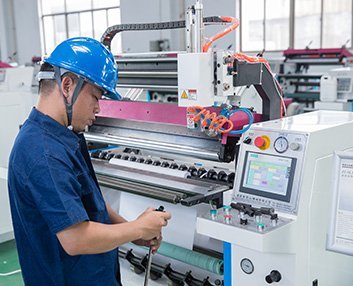
Installation and operation user manual, wire connection diagram, tension controller guide.
Installation and operation video tutorial.
One-on-one remote video call assistance.
On-site installation and operation guidance.
- Factory
- Customer
- Specs
Max. Unwinding Width | 1400mm |
Max. Unwinding Diameter | 1000mm |
Max. Rewinding Diameter | 300mm |
Min. Slitting Width | 25mm |
Max. Machine Speed | 300m/min |
Around 30-45 days, mainly depends on machine type.
Sure, it is our honor to work for you.
We will offer you some parts as backup, in case any part is broken within one year, we will sent you for free.
Sure, if we have client in your country, we will offer.
Unraveling the Journey of Thermal Paper Production and the Role of Cash Register Paper Roll Slitter
In the fast-paced realm of modern printing, thermal paper rolls hold a pivotal position, often overlooked despite their indispensability.
These unassuming rolls boast a remarkable technology: a specialized heat-reactive coating, eliminating the need for ink or ribbons for printing.
With diverse applications ranging from retail and point-of-sale systems to ticketing, labeling, and medical instruments, thermal paper rolls offer cost-effectiveness, printing speed, and unmatched print clarity, making them the preferred choice across various industries.
Nonetheless, environmental concerns loom due to the presence of chemicals like bisphenol A (BPA) in the coating. Addressing these issues, manufacturers now produce BPA-free thermal paper, emphasizing the importance of responsible disposal practices to mitigate environmental impact.
In the face of the digital age, thermal paper rolls continue to shine as a reliable and efficient printing solution, underlining their profound significance in modern-day operations.
The thermal paper production process involves several crucial steps, each executed with precision and dedication to excellence.
Step 1: Sourcing Sustainable Raw Materials
At the core of thermal paper production lies the sustainable sourcing of raw materials, primarily softwood trees such as spruce, fir, or pine.
These trees are thoughtfully cultivated in well-managed plantations that prioritize reforestation and the conservation of biodiversity.
By adhering to sustainable tree sourcing, the thermal paper industry plays a vital role in preserving our environment for future generations.
Step 2: Pulp Extraction and Refining
The journey from tree to thermal paper begins with pulping, a process that converts raw wood into pulp.
Two primary methods of pulping exist: chemical and mechanical.
Chemical pulping, often employing the Kraft process, involves cooking wood chips in a chemical mixture to remove lignin and effectively separate cellulose fibers.
Conversely, mechanical pulping utilizes mechanical force to separate fibers, resulting in a coarser pulp.
The choice of pulping method significantly impacts the properties of the thermal paper, highlighting the importance of thoughtful selection.
Following pulping, the obtained pulp undergoes a refining stage, where it is processed to enhance its strength and eliminate any remaining impurities.
This refining process plays a pivotal role in ensuring the pulp meets stringent quality standards, contributing to the overall excellence of the thermal paper.
Step 3: Bleaching and Enhancing Pulp Characteristics
Upon refining, the pulp may undergo a bleaching process to elevate its brightness and whiteness, essential for producing visually appealing thermal paper.
The extent of bleaching depends on the intended end-use and specific requirements of the product.
Step 4: Coating Application: Precision in Every Layer
One of the most critical and intricate steps in thermal paper production is coating application.
A specialized mixture comprising a colorless dye, a developer chemical, and a binder is uniformly applied to the paper’s surface.
This coating is meticulously engineered to ensure precise and consistent printing results when exposed to heat.
Coating thickness, chemical composition, and application techniques are all subjected to rigorous quality control measures, ensuring that the thermal paper exhibits superior thermal sensitivity, exceptional print clarity, and resistance to fading or smudging.
Step 5: Drying and Precision Winding
Following the coating process, the thermal paper is carefully passed through drying sections to eliminate excess moisture and firmly set the coating onto the paper surface.
Precision winding into large rolls or cutting into smaller sheets, depending on the intended application, ensures uniformity and efficiency in the production process.
Step 6: Quality Assurance and Testing
Before reaching the market, the thermal paper undergoes comprehensive quality assurance and testing procedures.
Stringent checks validate print clarity, durability, sensitivity to heat, and resistance to environmental factors.
These meticulous evaluations guarantee that the thermal paper not only meets industry standards but also exceeds customer expectations.
During thermal paper production at paper mills, large jumbo rolls with widths ranging from 636mm to 795mm are commonly avaibale from retailer.
However, for direct use in cash registers, banks, and hospitals, these jumbo rolls are impractical.
This is where thermal paper slitting machines come into play, bridging the size gap and transforming jumbo rolls into smaller, customer-ready rolls of various widths.
Thermal paper slitting machines offer unparalleled customization versatility.
Different industries require thermal paper rolls of varying widths to suit their specific needs, and these machines provide the flexibility to meet those unique demands while minimizing waste and maximizing efficiency.
Semi-automatic | High Speed Type | Fully automatic | |
Max unwinding width | 900mm | 900mm | 900mm |
Max unwinding diameter | 1000mm | 1000mm | 1000mm |
Max rewinding diameter | 160mm | 300mm | 300mm |
Max rewinding speed | 150m/min | 210m/min | 300m/min |
Loading | Chain | Hydraulic | Hydraulic shaftless |
Packing line | Yes | No | Yes |
(Please take noted: width can customize)
Three types of cash register paper roll slitter are available: semi-automatic, high-speed, and fully automatic, each with specific capabilities to cater to different production requirements.
The machines are equipped round slitter blade with advanced technology ensuring precision cuts and resulting in neatly trimmed thermal paper rolls without compromising print clarity or durability.
By owning a thermal paper slitting machine, businesses involved in thermal paper distribution and conversion significantly boost production efficiency.
This eliminates the need for outsourcing the slitting process, enabling better control over production timelines and the ability to respond swiftly to customer demands.
Consequently, overall productivity and customer satisfaction are enhanced, contributing to long-term growth and success.
Incorporating in-house slitting capabilities allows businesses to maintain strict quality control throughout the production process.
From selecting the finest raw materials to monitoring each step and conducting consistent quality checks, superior thermal paper rolls can be ensured.
Moreover, reducing reliance on external slitting services results in operational cost savings over time.
The world of paper converting holds boundless opportunities, and reselling small rolls offers a path to profitable growth.
We extend an invitation to take the leap into the slitting field and partner with us for an unparalleled experience.
Combining our industry expertise with your entrepreneurial spirit, we can craft a transformative production plan that sets you on the path to success.
Do not hesitate to contact us today, and let us embark on this promising journey in paper converting together.