Flexographic Printing Machine Manufacturer
- Ceramic Anilox cylinder, long life, wear resistance, corrosion resistance
- 360-degree registration adjustment
- Automatic web guiding system
- Optional video inspection system
Recoginze Flexgraphy Printer
Jota flexo printing machine was initially designed for printing graphics, logo.
Many kinds of substrates could be supported, such as paper, film, label.
Please contact us to design and customize your own flexographic printing machine.
Mexico Client Purchased Flexo Printing Machine from Jota
Jota Machinery: Professional Flexo Printing Machine Supplier in China
Jota is original flexo printing machine manufacturer, you could directly video call with us via WhatsApp.
We could lively show you Jota real-time factory and Jota flexo press demo.
Please speed up your hands to send us an inquiry, enjoy a real-time demo with us.
Jota CNC Center
Machining Material
- Visible high-quality components.
- Famous brands such as Siemens, Yaskawa, Delta, Schneider, Mitsubishi.
- Self-supporting CNC processed sheet metal, precision parts.
- Assembly raw materials provided by long-term cooperation suppliers.
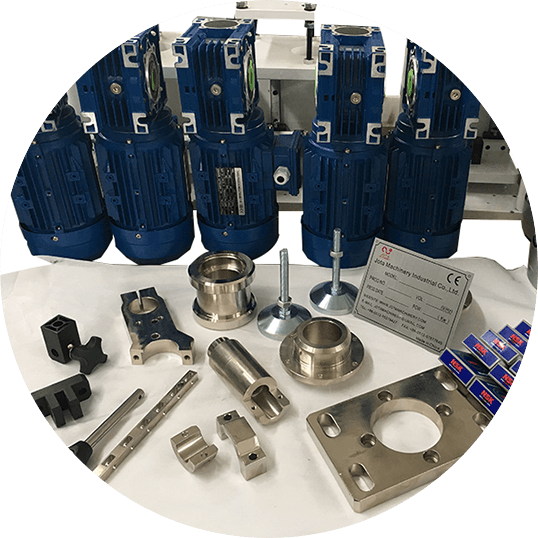
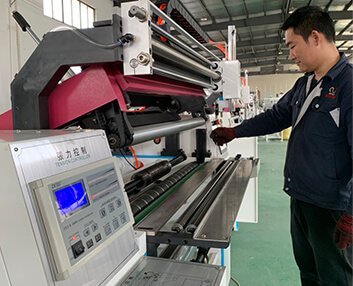
Installation and operation user manual, wire connection diagram, tension controller guide.
Installation and operation video tutorial.
One-on-one remote video call assistance.
On-site installation and operation guidance.
- Focus Factory
- Dear Customer
- Professional Team
Around 30-45 days, mainly depends on machine type.
Sure, it is our honor to work for you.
We will offer you some parts as backup, in case any part is broken within one year, we will sent you for free.
Sure, if we have client in your country, we will offer.
What is Flexographic Printing?
Last Update Time:12/04/2022 | Jota Machinery
Flexographic printing technology is easy visable in our surround environment , however, do you consider how does flexo printer working to print the colorful graphy?
In a world that has gone technological in every sphere of the economy, graphics has taken center stage in brand marketing.
A couple of printing techniques have evolved through unrelenting innovations. Top on the list is flexographic printing, also known as flexography.
Flexography is a type of rotary printing where flexible rubber printing plates apply ink to various surfaces.Inks used in this process dry fast through evaporation.
The Flexo press is the device responsible for the high-speed production of prints in this process.
The Flexo printing process is unique due to its ability to adapt to various materials. Such mediums include; carton board, paper, thin-film, in-mold, flexible packaging, latitude, and shrink sleeves.
The flexo technology is versatile in using UV and water-based inks. This article will discusses the flexo from below point
Technology Involved In Flexo Printing
The Flexo Press
Application Of Flexo Printing
Inks Used In Flexo Devices
How To Buy A Flexo Machine, And Much More
Read on for more details!
A brief history of flexo printing
Bibby & Baron, and sons made the first flexo patented machine in Liverpool in 1890. It used water-based ink. Other devices which used rubber printing plates came into use in the early 1900s in Europe. They used aniline oil-based ink, which led to aniline printing. The Germans developed machines whose printing process was called “gummidrunk.”
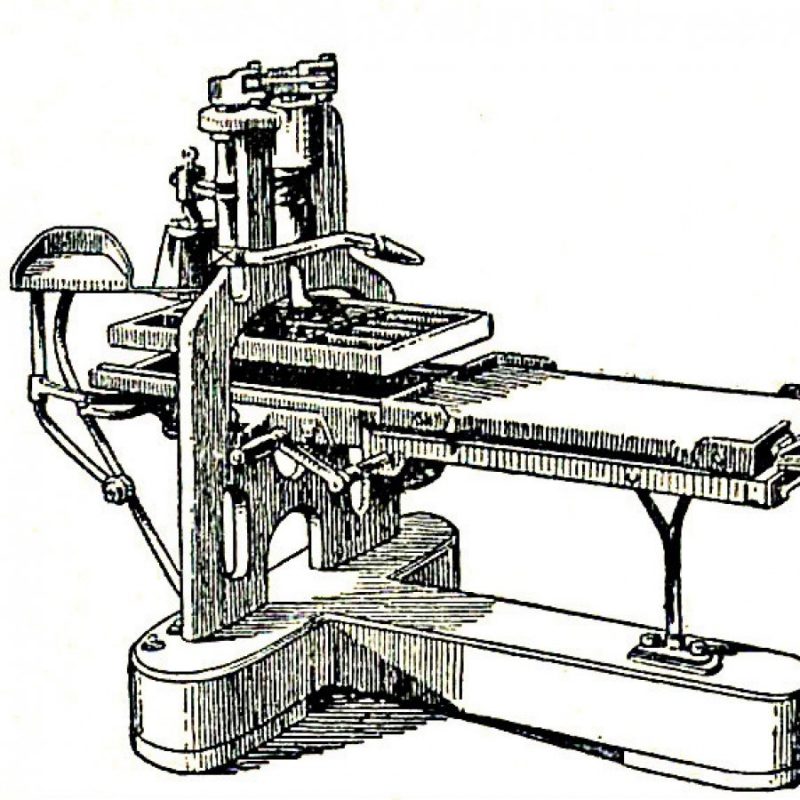
The “gummidrunk” technique was common in food packaging in the US. In the 1940s, FDA condemned aniline inks as unfit for food packaging.
Printing sales fell, and even with the emergence of safe inks, food industries turned against aniline printing.
This move called for the renaming of the food packaging printing. The industry players conducted a poll that proposed three names for the process.
The names were Permatone, Rotopake, and flexographic process. In 1951, the name flexographic process was overwhelmingly chosen.
Development of flexographic printing
In the beginning, flexo printing was rudimentary, and it applied the offset process. But since 1990, significant innovations have been seen in the ink systems and printing ink, flexo devices, and printing plates.
Advances have been made in photopolymer printer plates, methods of plate creation, and plate material. Technologies in the digital design of plate systems have emerged. Flexo printing can now produce total color products.
What is the flexographic printing machine
A flexo printing press is a piece of significant machinery behind producing labels at high speeds. It has several wheels that work harmoniously to pick ink from the reservoir, deliver it to a printing plate or die, and roll the ink to mark the material.
This machine prints packaging and labels in high volumes through a roll-feed web process. The flexo printing machine can produce five hundred to two thousand feet of rolls per minute.
Your flexo printing machine price can be as low as $2,1000 and as high as $ 50, 000, depending on size, use, color, and speed. You can get a full-color flexo printing press for a market price of $2,1000.
The four essential parts of the flexo press
Your flexo printing device prides itself on four significant sectors which work together to deliver world-class prints. They include:
- The Printing Section
- The In-Feed And Unwinding Section
- The Rewinding And Out-Feed Section
- The Drying Section
- The printing section. This part is home to the anilox, impression rolls, plate, and the single color section, including the ink chamber.
- The in-feed and unwind section. For the web to unwind appropriately, the roll of stock is held in control in this section.
- The rewind and out-feed section. Like in the unwind section, this device keeps the web tension under control.
- The drying station. In this part, specially formulated inks, high-speed hot air, and an after-dryer are applicable.
The flexo printing process overview
Flexographic printing involves three significant steps. These steps require expertise for high-end products and the efficiency of the process. The steps are essential in minimizing waste.
- Plate-making
- Mounting
- Printing
- Printing
Plate-making
The three methods of plate-making are:
- The use of the light-sensitive polymer. In this method, a film negative placed on the plate is exposed to UV light. Where the light passes through the film, the polymer hardens. The other polymer is washed in a mixture of water and one percent dishwasher soap at 40 degrees Celcius.
- Plate making. This method etches the image onto the printing plate using a computer-guided laser.
- The molding process. Firstly, a metal plate is created from the negative of the initial idea in an exposition procedure. The metallic plate is later used to make the mold in a plastic, glass, or bakelite board. After cooling, the mold presses the plastic compound or rubber to make the cliché or printing plate.
Mounting
A plate is made for each color and transferred to the cylinder, which is mounted on the flexo press.
To guarantee accurate pictures, mounting marks are made on the plates. Specialized devices are applied in ascending the plates on the cylinders to maintain registration.
The purpose of precise mounting is the consistent accuracy of prints.
Practical plate mounting can be realized by achieving an ideal bond and positioning the plate accurately.
Printing
Ink is moved from the ink roll to the ceramic registration or anilox during the printing process. The texture of the anilox holds a controlled amount of ink through small wells that meter ink uniformly to the printing plate.
The ink on the printing plate must not be excessive to achieve an even and quality print. The doctor’s blade scraps extra ink from the anilox.
Where UV curing ink is not used, the sheet is pressed through a dryer before its touched.
The operational overview of the flexo press
We give you a philosophical view of the operations of flexo printing devices in the following areas of interest.
- The Fountain Roller
- The Anilox Roller
- The Plate Cylinder
- The Impression Cylinder
- The Doctor Blade
The fountain roller
This component is responsible for transferring ink from the ink chamber to the anilox roller. The anilox roller is called a metering roller or a type of meter in modern flexographic printing.
The anilox roller
As earlier mentioned, the anilox roll is a unique character in flexography. This metering roller transfers an even thickness of ink to the printing plate. It is equipped with microscopic and finely engraved cells, also called wells, with a specific ink capacity.
The plate cylinder
This cylinder holds the printing plate using magnets, tape, ratchets, and tension straps against the plate cylinder. The printing plate is made of a rubber-like soft, flexible material.
The impression cylinder
This device exerts pressure on the plate cylinder when the image is being transferred to the substrate. It is also called the print anvil.
The doctor blade
This optional device scraps excess ink on the anilox, leaving ink only contained in the cells. Initially, doctor blades were made of steel.
But advanced blades made of polymer material are currently in use and have various beveled edges.
Pros of flexo printing
- It is suitable for long printing runs due to its high speeds.
- It delivers high-quality prints with minimum waste in a short period.
- It prints on different substrate materials.
- It eliminates the additional cost and work since varnishing, printing, die-cutting, and lamination are done in a single pass.
- It has a low cost of buying equipment and maintenance.
- It is a controlled and straightforward printing procedure.
- You don’t need high skilled operators to get high-quality output.
Think about your operational process, available space, and the skills needed to operate the press. Buy according to the size of your operations.
Functionality
The features in your machine are suitable for enhanced functionality. Buy a device with a different drying system, a web cleaner, a conveyor system, and an automated inking system. Think about your future press needs as the business grows.
Quality
Invest in a quality machine from a reputable manufacturer or supplier. Check customer reviews before you make your final decision on your preferred brand. A quality machine will create quality products for a happier customer.
Cost
Work within your budget. Be sure you are getting value for your money. The most expensive machine may not be the best quality. Remember, cheap can be very expensive.
When buying a flexographic printing press, avoid the following mistakes:
- Buying a machine that is over-equipped with surplus functions and features. Much your needs with your budget.
- Falling for a brand at the expense of a device that fits your needs.
- Buying cheap at the cost of a quality machine with longevity.
- Ignoring the aftersales services.
- Putting the machine to work before proper testing and training.
Common types of flexographic inks
Flexographic printing uses four standard inks. Your understanding of these inks and their appropriate applications is essential. The aim is to help you make the most of your flexo machineand satisfy your customer needs.
- Water-based
- Solvent based
- Ultraviolet and Electron Beam ( UV & EB)
- Oil Based
Water-Based
Water-based inks are made of pigment and water with various additives and agents and de-foamers. These additives facilitate the adhesion and drying processes.
Their other unique quality is that they have the most surface traction of all available ink types. Natural blends are the most common, but they are suitable for all elastomer types. They are
widespread in the corrugated packaging business.
Solvent Based
Solvent-based inks are composed of acetates, alcohols, and pigments are containing 80-90% alcohol. Acetates should have been between 10-20% of the solvent-based ink.
Their surfacetension is much lower than that of the water-based inks. This ink has an EPDM (ethylene propylene diene monomer) elastomer. It is commonly used in industrial films and plastic shopping bags.
Ultraviolet and Electron Beam ( UV & EB)
This ink type is composed of monomers, pigments, photoinitiators, and prepolymers. It adheres and dries when it is exposed to an electron beam or Ultraviolent light.
This ink is unique for its high consistency. It is resistant to ozone due to the component of EPDM elastomer. This ink type is safe and famous in the printing of outer wraps for food packaging enterprises.
Oil Based
Oil-based inks are components like pigments, hydrocarbons, and occasionally soy oils. Mineral oil is pretty used in the making of this ink.
Composite solvents like hexane and naphtha are very harsh. Â It is recommended that Buna/nitrile be used to manufacture the oil-based ink. This ink is commonly used in the publication printing sphere.
Depending on which industry you are involved with, you can now make an informed decision about your ideal ink for quality products. You may be interested to know that flexographic inks are divided into two classifications, namely, energy curable and volatile.
- Energy curable inks are cured when the ink dries on the substrate due to intermolecular bonding.
- Volatile inks have liquid solvents like alcohol or water. This solvent evaporates and leaves the image on the substrate.
Applications of the flexo press
So far, you are well versed with flexography. This technology is ideal for modern printing needs since it can use a variety of inks. It can print on foil, plastic, brown paper, acetate film, and other packaging materials. Common brands published by flexo devices are:
- Food and hygiene sacks and bags
- Flexible plastics
- Retail and shopping bags
- Milk and beverage cartons
- Disposable cups and containers
- Envelops and wallpaper
- Self-adhesive labels
From the list above, it is proper to hold that flexo printing is standard in the food industry.
Conclusion
Compared to other printing techniques, flexographic printing is very affordable, efficient, and fast. If you are in the food industry, go for wrapper and packaging material products done through this process. They are safe for your consumers and eco-friendly.
If your concern is to venture into the printing business, you are better equipped to buy the best printing equipment based on your budget and needs. If you have been in the printing sector and want to expand your company, flexo machines are your ideal partner.
For more information contact us or visit our website.